Staying Safe: 5 job site tips from L&W Supply
L&W Supply, the Chicago-based building materials distributor, has created a list of measures to help promote safety on the job site.
According to L&W, safety should always be the number one priority of anyone who steps foot on a job site, especially the workers. With the advent of new social distancing guidelines, on top of existing hazards on a job site, safety is more of a challenge than ever before.
Here are five safe practices from L&W Supply:
Practice Safe Social Distancing: In order to keep you, your team, and your family members safe during this time, it’s important to follow CDC guidelines and practice social distancing while working on a job site. This means keeping 6 feet apart from others wherever possible. They recommend refraining from handshakes, fist-bumps, or other forms of contact. If you or a team member is feeling under the weather, it’s important that they stay home until they are feeling better. The CDC has also recommended that individuals wash their hands often, cover their nose and mouth with a cloth, and clean and disinfect any frequently touched surface daily.
Know the job site – and the schedule: One of the first steps you should take is to become familiar with the layout and the schedule for deliveries and work to be done on the site. Rather than having to react to an incident after the fact, management and associates should work to identify and solve potential safety issues before they occur.
“A job site is an ever-changing work in progress, with various moving parts and people filtering in and out during the day,” said Heath Pellegrin, branch manager for L&W Supply in Beaumont, Texas. “As the site evolves, new concerns can arise that were not present before, making it especially important to know the schedule in and out.”
In order to accomplish this, take a look at the project’s schedule. Identify the potential safety hazards that each phase of the project will present and determine the best way to mitigate those risks, keeping in mind that these hazards will change as the project continues. The more information you and your team can have at their fingertips, the better equipped you’ll be to make the right safety decisions.
Institute a cell phone policy: Cell phones have permeated every aspect of our personal and work lives, with the construction industry being no different. With the ability to send photos of jobs in progress, view site plans, and instantly communicate deliveries and orders, mobile technology has been a game-changer in terms of the way construction associates communicate with each other. The question then becomes: how can you limit distractions and keep people safe?
Using their best judgment, management will have to determine the risks and properly communicate to your team what the expectations are for mobile usage. Following basic OSHA guidelines, such as not using devices while operating machinery is essential, but beyond that, it is up to the discretion of the manager to determine the best cell phone policy to keep everyone safe.
Supervise your team: While safety should be practiced by everyone on a jobsite, it is important that there is one individual who is ultimately responsible for ensuring that a safety plan is executed. Since roles on a jobsite can change from project to project, it is crucial that whoever is in charge – be it a site superintendent, general contractor or other supervisor – keeps an eye on workers throughout the day. These efforts often require the coordination of more than one employer. Depending on the size of the project, wearables, cameras, and drones are also another great way to monitor workers.
For some jobs, consider using a buddy system that pairs more experienced workers with newer associates. This can not only help keep everyone safe, but also provide mentoring for younger associates.
Training and leadership: The strongest factor in ensuing safety among your associates is to properly train them in the first place. Workers need to be trained in order to be able to identify potential safety hazards and understand control measures that could be implemented to keep them safe. This includes temporary and contract workers, along with supervisors and management.
“At the end of a day, you can’t be everywhere at once, so the absolute best way to keep your workers safe is to lead by example,” said Linn Wayment, L&W Supply branch manager in Logan, Utah. “Some mistakes will happen, but in the hands of a knowledgeable team, the results will be a lot easier to manage.”
A culture of safety does not happen overnight, and what L&W has found is that the best way to inspire your workers is to practice what you preach. This is why it is just as important for management to understand worker’s rights and their own responsibilities in keeping their team safe.
L&W is a subsidiary of ABC Supply and operates about 175 branches in 35 states with a focus on distributing wallboard, suspended ceiling tiles, steel studs, joint treatment, insulation, fasteners and related building products.
According to L&W, safety should always be the number one priority of anyone who steps foot on a job site, especially the workers. With the advent of new social distancing guidelines, on top of existing hazards on a job site, safety is more of a challenge than ever before.
Here are five safe practices from L&W Supply:
Practice Safe Social Distancing: In order to keep you, your team, and your family members safe during this time, it’s important to follow CDC guidelines and practice social distancing while working on a job site. This means keeping 6 feet apart from others wherever possible. They recommend refraining from handshakes, fist-bumps, or other forms of contact. If you or a team member is feeling under the weather, it’s important that they stay home until they are feeling better. The CDC has also recommended that individuals wash their hands often, cover their nose and mouth with a cloth, and clean and disinfect any frequently touched surface daily.
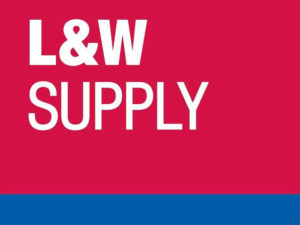
“A job site is an ever-changing work in progress, with various moving parts and people filtering in and out during the day,” said Heath Pellegrin, branch manager for L&W Supply in Beaumont, Texas. “As the site evolves, new concerns can arise that were not present before, making it especially important to know the schedule in and out.”
In order to accomplish this, take a look at the project’s schedule. Identify the potential safety hazards that each phase of the project will present and determine the best way to mitigate those risks, keeping in mind that these hazards will change as the project continues. The more information you and your team can have at their fingertips, the better equipped you’ll be to make the right safety decisions.
Institute a cell phone policy: Cell phones have permeated every aspect of our personal and work lives, with the construction industry being no different. With the ability to send photos of jobs in progress, view site plans, and instantly communicate deliveries and orders, mobile technology has been a game-changer in terms of the way construction associates communicate with each other. The question then becomes: how can you limit distractions and keep people safe?
Using their best judgment, management will have to determine the risks and properly communicate to your team what the expectations are for mobile usage. Following basic OSHA guidelines, such as not using devices while operating machinery is essential, but beyond that, it is up to the discretion of the manager to determine the best cell phone policy to keep everyone safe.
Supervise your team: While safety should be practiced by everyone on a jobsite, it is important that there is one individual who is ultimately responsible for ensuring that a safety plan is executed. Since roles on a jobsite can change from project to project, it is crucial that whoever is in charge – be it a site superintendent, general contractor or other supervisor – keeps an eye on workers throughout the day. These efforts often require the coordination of more than one employer. Depending on the size of the project, wearables, cameras, and drones are also another great way to monitor workers.
For some jobs, consider using a buddy system that pairs more experienced workers with newer associates. This can not only help keep everyone safe, but also provide mentoring for younger associates.
Training and leadership: The strongest factor in ensuing safety among your associates is to properly train them in the first place. Workers need to be trained in order to be able to identify potential safety hazards and understand control measures that could be implemented to keep them safe. This includes temporary and contract workers, along with supervisors and management.
“At the end of a day, you can’t be everywhere at once, so the absolute best way to keep your workers safe is to lead by example,” said Linn Wayment, L&W Supply branch manager in Logan, Utah. “Some mistakes will happen, but in the hands of a knowledgeable team, the results will be a lot easier to manage.”
A culture of safety does not happen overnight, and what L&W has found is that the best way to inspire your workers is to practice what you preach. This is why it is just as important for management to understand worker’s rights and their own responsibilities in keeping their team safe.
L&W is a subsidiary of ABC Supply and operates about 175 branches in 35 states with a focus on distributing wallboard, suspended ceiling tiles, steel studs, joint treatment, insulation, fasteners and related building products.