BMC Builds a Dream Team
BMC’s impact on the LBM industry is cover-story worthy for many reasons. Let’s count them: the strategy of expansion and acquisition; the double- digit sales growth; the business-building innovations — perhaps illustrated best by the company’s fast-growing READY-FRAME offering, a pre-cut and pre-labeled framing program that delivers time-saving solutions to the job site. Then there’s the realization of operational synergies with the BMC, Stock Building Supply merger and the hiring of a new CEO.
But when asked to talk about the company, the people who run it tend to talk first about something entirely different — the culture. And in this regard, BMC has set an extremely high bar.
“We want our people to drive to work with more excitement than when they drive home,” said COO Mike McGaugh. “You can’t have a fear-driven organization and be able to accomplish that. You need to have a performance- driven organization, one that’s focused on getting a little better every day.”
How does BMC encourage that kind of commute for employees? The answer’s taken several years to cultivate, but recently, the company hit a cultural milestone during their leadership meeting in March 2018. That’s when three new major culture-related programs were formally injected into the organization.
- The official corporate embrace of the principals of servant leadership as outlined in the best- selling book The Servant: A Simple Story About the True Essence of Leadership.
Effectively, this announcement turned the management charge upside down, with the CEO on the bottom serving the employee and the employee serving the customer on the top. Asked how he felt about being on the bottom of the inverted pyramid in a culture of servant leadership, CEO David Flitman told HBSDealer that he not only liked it, it’s one of the reasons he came to BMC in the first place. “In my view, the leader’s role is to serve the organization,” he said. “It’s to remove barriers. The leader’s role is to make sure the organization is collaborating, and we’re doing what we need to do for the customer.”
- The introduction of the BMC Dream Team, an internal program that gets leadership in a room to vote on high-performing, over-achieving individuals to be recognized throughout the organization on a weekly basis.
Honorees range from Colorado Outside Sales Rep Freddy Florez, whose enthusiasm for READY-FRAME led to the solution being affectionally dubbed “Freddy Frame” at the local level, to Office Manager Yara Gomez, who earned distinction by filling in as a truss plant manager and increasing productivity by 30% during her first two days in the interim position. (See sidebars: “Dream Team Profiles”)
- Programs one and two are subsets of a larger corporate initiative: the introduction and branding of the BMC Operating System.
The operating system isn’t a piece of software that can be uploaded to a computer; rather, it’s an ever- evolving physical guidebook focused on people, process and performance. It’s described as a program that uses lean principles to identify opportunities and create best practices to improve service, increase efficiencies and remove costs from the business.
Human Resources SVP Mike Farmer looks back at the March leadership meeting and its cultural initiatives as a significant moment for the company. “That set the tone for the year and really set the tone for our culture,” Farmer said. “We reached the point where we solidified the culture. Now we plan to build on it.”
“That March meeting was a big day,” said Bert Stephens, BMC’s VP of Operational Excellence and developer of the BMC Operating System. “It energized the company. Once we introduced the operating system and unveiled servant leadership, and the training, we as a company doubled down on investing in our people and giving them the tools needed to succeed.”
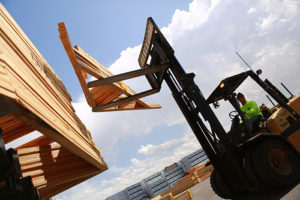
If printed out and placed in a binder, as it often is, the BMC Operating System runs about 120 pages. A key feature of the system is its fluidity.
As the company learns, the system is updated in a continuous cycle of improvement. “If it’s not a living document, then it becomes stagnant,” he said. “And if it’s stagnant, then I don’t know why we’d be wasting our time on it.”
So, what’s in it? In developing the program, Stephens, who describes himself as a “shop rat” with a career grounded in practical application of best practices to operations, says he borrowed from Lean Six Sigma and other operating systems that guide companies such as Toyota and Ingersoll Rand. “I kind of took the best of all that was out there and tailored it for BMC,” he said.
Spreading the gospel of the system are 22 specially trained BMC lean leaders.
An interesting and memorable character in the BMC playbook is TIM WOODS. His name is an acronym for the eight wastes to avoid when establishing a highly efficient building material organization. (For instance, T stands for Transportation waste — frontline employees are trained to identify wasted or unnecessary movement of materials from place to place.)
Borrowing from the lean manufacturing mindset, the operating system also promotes the five S methodology: Sort, Straighten, Sweep, Standardize and Sustain. The company added the ever- important Safety as a sixth S.
Before the introduction of the formal operating system, BMC was able to do many things well. But according to Stephens, what the system brings is a way to leverage operational excellence across the organization. He draws a comparison to winning in football. “If you’re a team with a West Coast offense, and it’s fourth and one, here’s what you do,” he said. “In the same way, we use the BMC Operating System as our playbook.”
BMC executives are watching the scoreboard light up.
“It’s easy to see the results of the system, and the impact is dramatic,” said McGaugh. “We’re winning more with our customers. Our service levels are higher. Our safety rates and incident rates are lower. Everybody wins with this.”
# # #
The January issue of HBSDealer features a special report cover story on BMC. Check out the issue here in the HBSDealer archive.